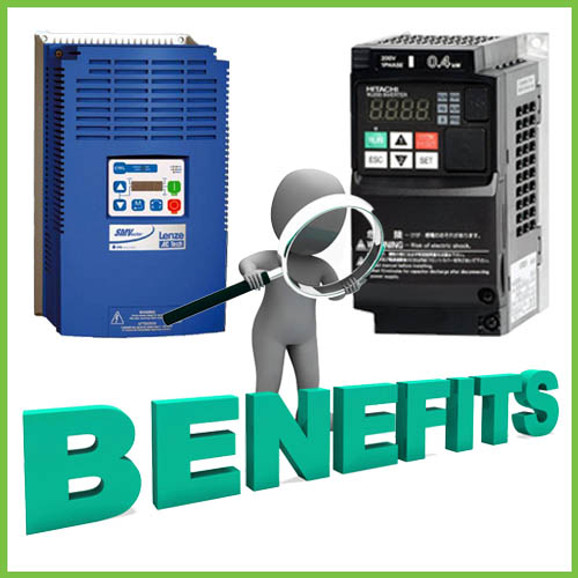
What are the Benefits of a Variable Frequency Drive?
Posted by Theresa Hoffman on Dec 6th 2023
Since the primary purpose of a VFD is precise SPEED CONTROL so that motor speeds can be ramped up and ramped down and the connected load can be maintained at the required speeds, which only utilizes the energy required. Knowing this, we wanted to breakdown the tangible and intangible benefits of installing a VFD.
Controlled Starting Current
When an AC motor is started “across the line,” it can take up to as much as seven-to-eight times the motor full-load current to start the motor and load. This current flexes the motor windings and generates heat, which will, over time, reduce the longevity of the motor. An VFD Drive starts a motor at zero frequency and voltage. As the frequency and voltage "build", it "magnetizes" the motor windings, which typically takes 50-70% of the motor full-load current. Additional current above this level is dependent upon the connected load, the acceleration rate and the speed being accelerated, too. Bottom line...this extends motor life!
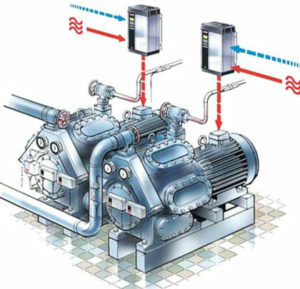
Reduced Power Line Disturbances
Starting an AC motor across the line, and the subsequent demand for 300-600 % the motor full-load current, places an enormous drain on the power distribution system connected to the motor. When the supply voltage sags, depending on the size of the motor and the capacity of the distribution system, the voltage sags can cause sensitive equipment connected on the same distribution system to trip offline due to the low voltage. Items such as computers, sensors, proximity switches, and contactors are voltage sensitive and, when subjected to a large AC motor line started nearby, can drop out. Using VFD eliminates this voltage sag, since the motor is started at zero voltage and ramped up
Lower Power Demand on Start
If power is proportional to current-times-voltage, then power needed to start an AC motor across the line is significantly higher than with a VFD. This will be true only at the start up. The primary issue is that some electrical distribution systems might be at their limit during specific times of day, usually considered “Peak Hours.” When industrial customers start their motors during these peak hours of electrical consumption, it is not uncommon for the customer to be stung with charges for surges in power during peak periods. These demand factors would not be an issue with VFD’S.

Controlled Acceleration
A VFD starts at zero speed and accelerates smoothly on a customer-adjustable ramp. Conversely, an AC motor started “across the line” triggers higher mechanical shock loads both for the motor and mechanically connected load. This shock will, over time, increase the wear and tear not only on the connected load but the AC motor as well. Applications that include easy-to-tip product, such as bottling lines, greatly benefit from a slow ramp up in power which allows the conveyor belt to smoothly speed up rather than an abrupt jerk to full power.
Adjustable Operating Speed
Unlike the traditional stop-and-go motor, the use of a VFD enables optimizes a process, by making changes in a process. This allows starting at a reduced speed, and allows remote adjustment of speed by programmable controller or process controller. Control, in an industrial sense, is always a big bonus for production!
Adjustable Torque Limit
Use of a VFD can protect machinery from damage and protect the process or product (because the amount of torque being applied can be controlled accurately). An example would be a conveyor jam. If just an AC motor connected, the motor will continue to try to rotate until the motor’s overload device opens (due to the excessive current being drawn as a result of the heavy load). A VFD, in turn, can be set to limit the amount of torque (AMP/CURRENT), so the AC motor never exceeds this limit.
Controlled Stopping
Is just as important as controlled (ramped) acceleration, controlled (ramped) stopping can be important to reduce mechanical wear and tear — due to shocks to the process or loss of product due to breakage.
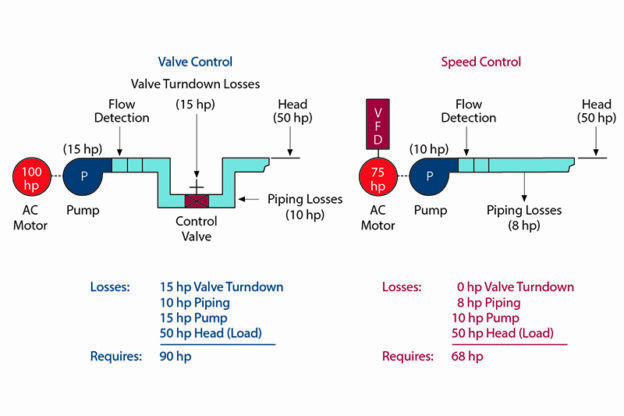
Energy Savings
Variable torque loads, such as, Centrifugal fans and pump loads operated with a VFD will reduces energy consumption. Centrifugal fans and pumps follow a variable torque load, which has horsepower proportional to the cube of speed and torque varying proportional to the square of speed, also known as the “Affinity Laws”. Example; if the speed of a fan is cut in half, the horsepower needed to run the fan at load is cut by a factor of eight (1/2)3 = 1/8. In trying to duplicate this advantage with standard inductive motor would require some type of mechanical throttling device, such as a vane or damper; but the motor would still be running full load and full speed (full power). Example: A VFD controlling a pump motor that usually runs less than full speed can substantially reduce energy consumption over a motor running at constant speed for the same period. For a 25 horsepower motor running 23 hours per day (2 hours at 100% speed; 8 hours at 75%; 8 hours at 67%; and 5 hours at 50%) a variable frequency drive can reduce
energy use by 45%. At $0.10 per hour kilowatt hour, this saves $5,374 annually. Because this benefit varies depending on system variables such as pump size, load profile, amount of static head, and friction, it is important to calculate benefits for each application before specifying a VFD. Savings of a VFD can be sufficient which would allow for shortened payback period.
Reverse Operation
Using a VFD eliminates the need for a reversing starters, a VFD allows electronic ability reversing either by integrated reversing or an external switch added to the VFD terminal control board. The elimination of a reversing starter eliminates its maintenance cost and reduces panel space.

Elimination of Mechanical Drive Components
Using a VFD Drive could potentially eliminate the need for expensive mechanical drive components such as gearboxes. Because the VFD can operate with an infinite variable speed, it can deliver the low- or high-speed required by the load, without a speed-increasing or reduction devices between the motor and load, of course this is application dependent. This eliminates maintenance costs, as well as reducing floor-space requirements.
Still curious about how incorporating a VFD could benefit you? Take a look at our “Making Greywater Greener” blog which dives further into the benefits of including a VFD in any wastewater treatment center. You could also check out our helpful blogs on “Basic VFD Programming Tips“, “What is a Drive?” or “Phase Converters vs. Variable Frequency Drives” to learn even more about VFDs and their benefits.
If you’re ready to take advantage of installing a VFD for your application, contacts our sales team or tech support today and we’d be more than happy to help you with sizing, price and availability!