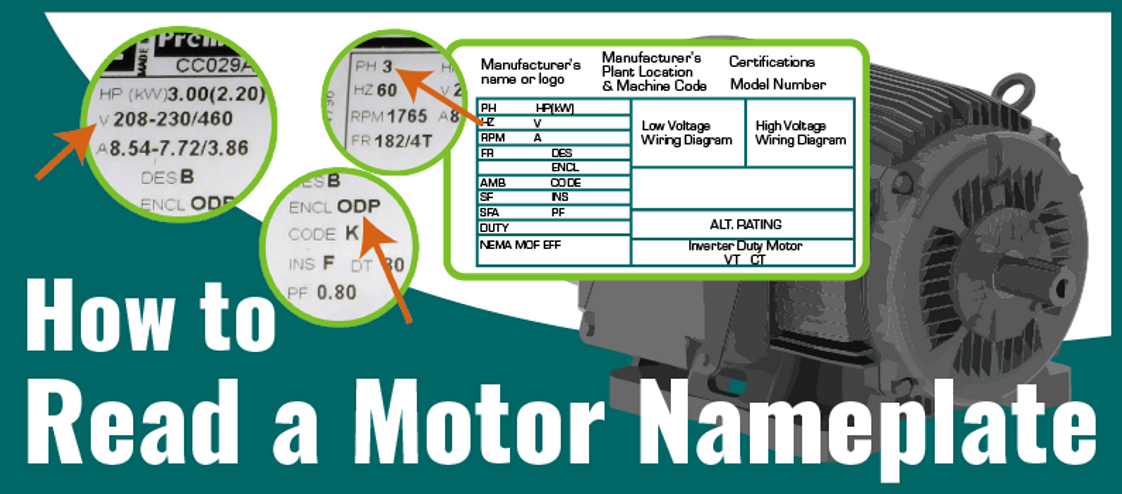
How to Read a Motor Nameplate
Posted by Morgan Spano on Aug 30th 2022
Ordering an electrical motor can seem complicated, but understanding the nameplate may save you some confusion.
Motor nameplates in North America are required to supply certain electrical specifications thanks to the National Electrical Manufacturers Association (NEMA).
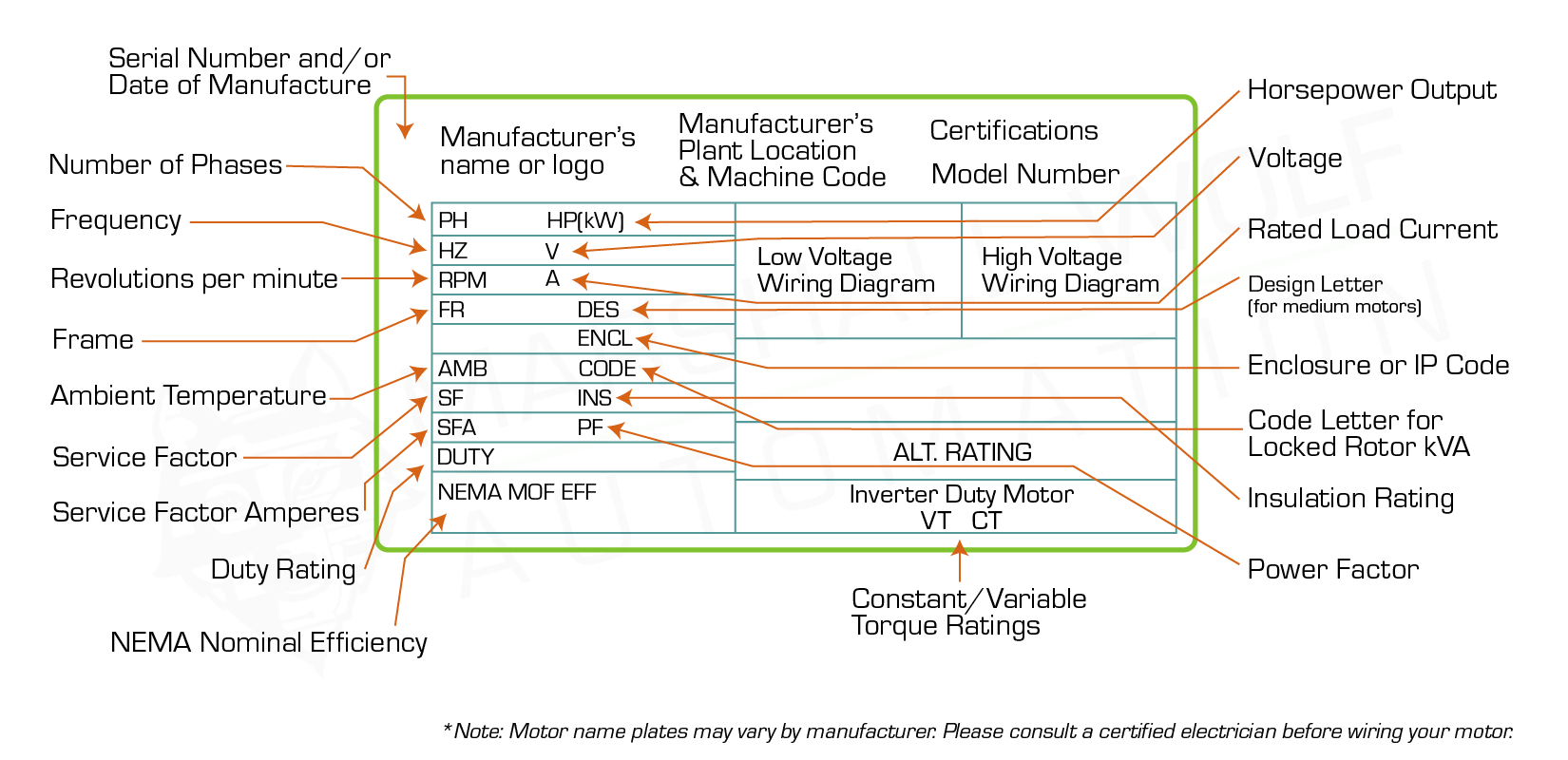
These standards make the motor selection process a matter of checking off your list of application needs.
NEMA Electric Motor Nameplate Requirements:
- Manufacturer’s name, mark, or logo
- Manufacturer’s plant location
- Manufacturer’s machine code
- Manufacturer’s model number or catalog number
- Serial number or date of production
- Enclosure or IP code
- Method of cooling or IC code
- Applicable rating and performance standard(s): e.g., NEMA MG 1 or IEC 60034-1
- Maximum momentary overspeed
- For AC machines, the rated power factor
- Maximum ambient temperature if other than 40°C
- Minimum ambient temperature
- Maximum water temperature for water-air-cooled machines if greater than 25°C
- Altitude if greater than 3300 ft (1000 m)
- Connection diagram located near or inside the terminal box
- Approximate weight of the machine, if exceeding 66 lbs. (30 kg)
What do all those abbreviations mean? Check out our handy guide to NEMA’s markings!
AC Motors
Pros:
- Simple to build
- Economical due to lower start-up consumption
- Study construction generally means a longer lifespan
- Generally, requires little maintenance
- Better for variable speed applications
Cons:
- Simple design means additional equipment may be required
- Speed control functions can be costly
DC Motors
Pros:
- Accurate and fast
- Speed can be controlled by varying the supply voltage
- Easy to install
- Starting torque is high
- Starting, stopping, accelerating and reversing are done quickly
Cons:
- Less common because they are less suitable for applications requiring high power
- They are made up of many parts that wear out and are expensive to replace
Stepper Motors
Pros:
- Accurate
- Inexpensive
- Study, simple construction
- High starting torque
Cons:
- Speed and torque are low compared to other motors
- Torque decreases sharply as speed increases
- Has the potential to overheat
- Stepper motors generate vibrations which can create resonance issues
Manufacturers often separate motor types by “catalog”, “family”, or “series” name and will convert that information into an individualized sku. This is where reviewing the machine code, model/catalog number or serial number displayed on the name plate comes in handy.
Phase, Current Input, Voltage and Frequency
How’s your motor going to be powered? While some motors may function utilizing batteries, most require either single or 3-phase input. In residential areas, it’s common to only have single-phase power available whereas industrial infrastructures commonly have access to 3-phase input. The solution to running a 3-phase motor on single phase power is to incorporate products such as a VFD or phase converter. Mind you, not all locations have the capacity to safely operate high voltage machinery and we recommend contacting a certified electrician before installation.
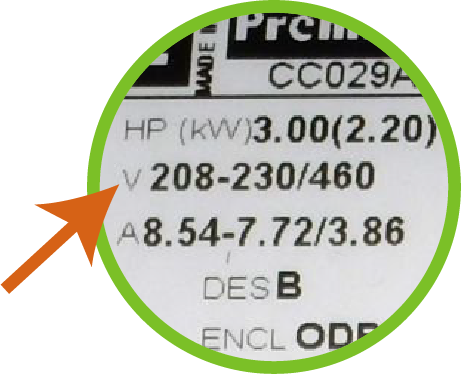
It’s equally important to properly specify the operating voltage and input current. Voltage refers to the constant flow of current to the motor while the current is the amount of electrical current withdrawn from the motor under normal loads. North American voltage standards are rated as 115/230V, 230/460V, 208-230/460V, and 575V and currents are measured in Amps. Operating a motor with improper voltage or current ratings has the potential to cause overheating, underperformance or even complete motor failure.
The primary consideration with frequency is where the motor will be operated. European AC Power standards for the alternating current value of the motor input current are 50 Hz while North American AC power utilizes 60 Hz.
Many motors offer the option for either 50/60 Hz frequency, but not every model does so; making it important to double check before purchase.
Horsepower, Torque and Speed
Knowing how fast you need the motor to run, how much force it needs to exert and how quickly it needs to be running at full capacity are all major factors. There are a few sources available to assist users in calculating electric motor amps, horsepower, and 3-phase kVA; but it is always recommended to consult with a certified electrician.
After determining the minimum required horsepower and RPM (revolutions per minute), it’s recommended to increase the rated torque values by 140%. You can think of it as a way to give your motor a little slack rather than having it run at the full capacity all the time. Just like any person; if you run your motor at full tilt consistently, you’re bound to have breakdowns.
Once you’ve determined the motor type, load and input characteristics, enclosure and mounting come into play.
Motor Enclosures and Mounting
What type of environment your motor is going to be functioning in? Is it going to be installed indoors or outdoors? Does it need protection from condensation, dust, or corrosive materials? Is there anything hazardous on the job site or is this a food application? Certain motors will even have ambient temperature requirements or elevation specifications to consider. To address these factors, you’ll want to figure out what type of enclosure and cooling is right for you.
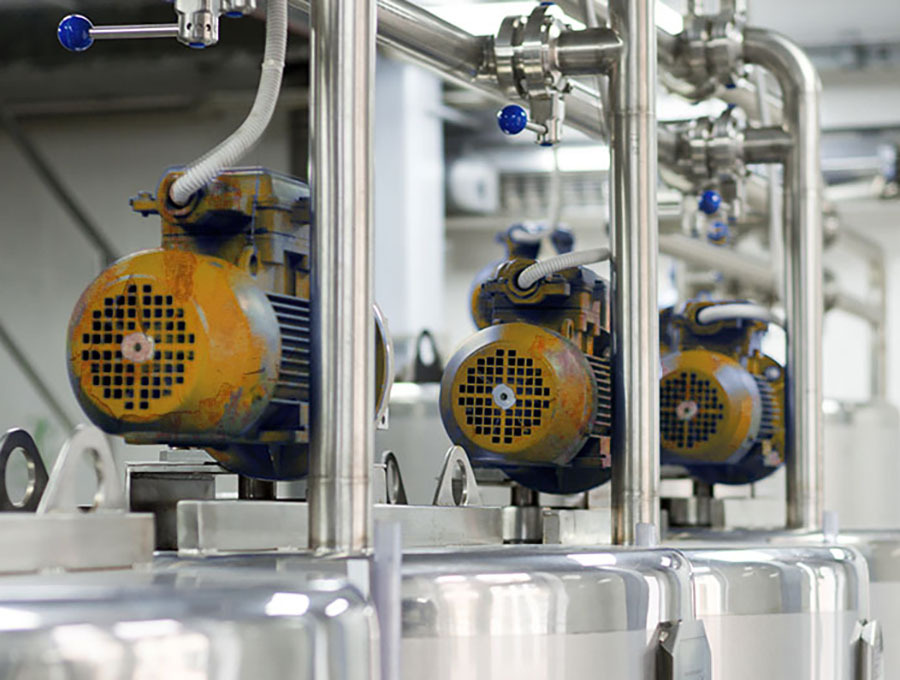
The most common types of motor enclosures are:
- Open Drip-Proof (ODP): Designed for reasonably dry, clean, and well ventilated (usually indoors) areas. Outdoors installation require the motor to be protected with a cover that does not restrict the flow of air to the motor.
- Totally Enclosed Air Over (TEAO): Dust-tight fan and blower motors for shaft mounted fans or belt driven fans. The motors are mounted within the airflow of the fan.
- Totally Enclosed Non-Ventilated (TENV): No ventilation openings, enclosed to prevent free exchange of air (not airtight). Suitable for projects where the motor is exposed to dirt or dampness.
- Totally Enclosed Fan Cooled (TEFC): Same as TENV with the addition of an external fan integrated into the motor design. The fan provides cooling by blowing air on the outside of the motor.
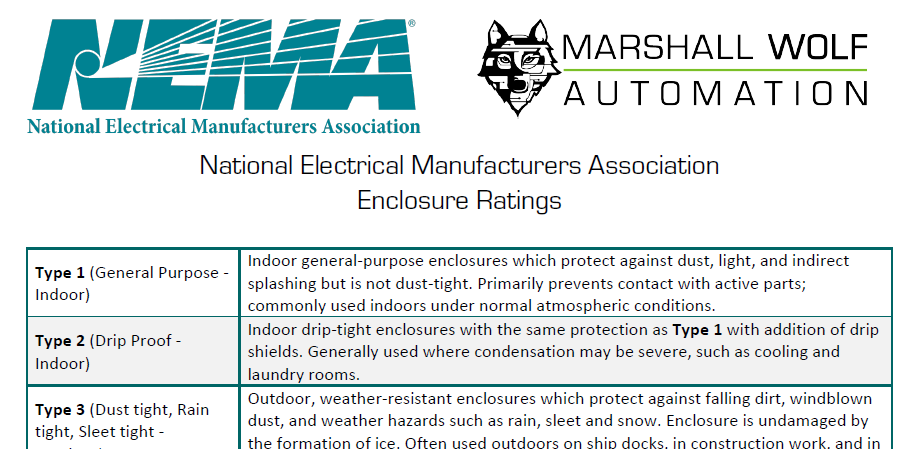
Knowing what type of enclosure is only the first half of the process, finding out the proper frame size and mounting will also affect your final motor selection. In North America, we use NEMA’s frame size standardization which is directly related to the horsepower, speed and type of enclosure.
Did you realize there was so much information packed into a motor’s nameplate? With a little decoding you’ll be able to look at any motor and understand the specifications required to have it up and running. Marshall Wolf Automation carries a wide variety of motors from manufacturers like Weg and Teco Westinghouse. Find yours today!